镁碳砖的生产工艺主要包括泥料制备、坯料成型、干燥硬化处理3个主要过程。
1、泥料的制备
在有高压力成型设备的条件下,镁砂的临界颗粒趋向于微细化。目前,我国成型设备压力较低,为了提高体积密度,许多厂家使用的临界粒度都在5mm以上。
骨料颗粒细微化,使开口气孔率变小,因而有助于提高镁碳砖制品的抗氧化性能,但是骨料直径变小,会使闭口气孔增加,体积密度降低,造成成型上的困难。
根据使用部位的不同,镁碳砖中的石墨和添加剂也不相同,如石墨加入量增加,制品的抗渣性和抗热震性能提高,但强度和抗氧化性能降低。
镁碳砖制品中如碳含量小于10%,镁碳砖制品不能形成连续的碳网,从而不能有效的发挥碳的优势。反之,如石墨量加入过多,生产时成型较困难,而且镁碳砖制品易氧化。因此,镁碳砖中的石墨加入量一般在10%~20%范围内。
在混练过程中,为了使石墨能均匀的包围在镁砂颗粒周围,加料顺序一般为镁砂颗粒——结合剂——石墨——镁砂细粉和添加剂的混合细粉。
由于配料中石墨含量大且比重小,添加剂的加入量又非常小,欲使之混合均匀,需要较长的混合时间,但混合时间过长又容易使镁砂颗粒周围的石墨和细粉脱落,因此混练时间要适中。目前,采用新型结构的高速高效混合机,其混合时间可缩短。另外,泥料的混合最好在带有加热装置的混练设备中进行。这样,树脂的流动性能好、能达到均匀分布的目的。
2、制品成型
镁碳砖制品成型是提高真空密度,使制品组织结构致密化的重要因素。因此,须采用高压力成型。另外,由于泥料中石墨加入量大,且泥料临界颗粒小,成型比较困难。因此,成型时应严格按照先后轻重,逐渐加压的操作规章流程进行压制,以免产生成型裂纹,最好采用抽真空,排气加压的操作规程。
真空脱气压砖机,是把装有泥料的砖模在真空状态下脱气后进行压制成型,由于成型前,成型的泥料间存在的空气几乎被真空泵吸出,因此成型几乎不产生裂纹,特别适用于压制石墨加入量多的材质。
由于镁碳砖中石墨含量高,近年来又倾向于临界颗粒微细化,成型采用高压力压砖机,因此砖坯及镁碳砖制品外形非常光滑,搬运和运输及砌筑时易产主滑动。成型后的砖坯须进行防滑处理,即砖坯可在热硬性树脂中?渍或布一层0.1~0.2mm的热硬性树脂。
3、干燥硬化处理
成型后的砖坯需要进行干燥,以提高常温下的机械强度。试样在低于250℃温度下处理具有较高的常温耐压强度,大于250℃处理的试样,其常温耐压强度有明显下降。试样在200~250℃温度下处理有较低的气孔率;低于200℃或高于250℃处理的试样,体积密度均有下降;相比之下,高于250℃处理,试样的体积密度降低更为明显。所以,镁碳砖一般在200~250℃的温度下处理,可得到性能较好的制品,升温速度应按下述规律进行。
50~60℃,因树脂软化,应保温;
100~110℃,溶剂大量排除,应保温;
200℃或250℃,为使反映完全,应保温。
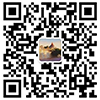