影响回转窑耐火材料使用寿命的因素很多,但主要是机械应力作用、热应力作用和生产操作这三个方面。逐一分析了这三方面因素对窑内耐火材料使用寿命的具体影响;在此基础上提出了延长窑衬寿命的管理和技术措施。
问题的提出
目前,我国的新型干法预分解窑生产技术已经成为水泥工业的发展主流,且已经进入大型化的发展通道, 5000t/d 及其以上规模的生产线是建设主流。众所周知,在煅烧过程中,熟料的烧成温度约为 1450 ℃,但窑内烧成带燃烧气体的温度最高可达 1700℃以上。如此高温的条件,对回转窑用耐火材料的要求也越来越高。
回转窑用耐火砖,其主要作用是避免窑筒体高温变形、减少热量损失、避免烧成过程中熟料对筒体直接地磨蚀、化学侵蚀等作用,从而延长窑的使用寿命。根据窑内不同带的温度,可以选择不同品种的耐火材料。但因回转窑是有一定倾角的旋转体镶砌在窑筒体内的耐火砖,在生产过程中,耐火砖因受机械负荷、热负荷和化学侵蚀等综合作用,过早的损坏而缩短使用寿命的情况会经常出现。因此,如何通过技术措施与控制,延长耐火材料使用寿命,以提高窑的运转率、降低耐火材料用量、提高熟料的产质量,降低生产成本,为水泥企业所关注。
耐火材料使用寿命的影响因素
影响窑内耐火砖使用寿命的因素很多,见图1。通过理论分析结合实际生产经验,认为主要是三个方面,即机械应力作用、热应力作用和生产操作的影响。
机械应力对耐火砖使用寿命的影响
机械应力是物体由于外因变形时,在物体内各部分之间产生相互作用的内力,以抵抗这种外因的作用,并力图使物体从变形后的位置回复到变形前的位置。当窑内耐火砖所承受的机械应力超过其自身强度时,砖体在应力作用下产生局部或全部损坏。
产生机械应力的主要因素有以下两个原因:
(1)椭圆变形。由于回转窑内衬砖、窑料和筒体自身重量等综合因素造成窑筒体变形,在重力以及热负荷作用下,筒体的圆形截面变成椭圆形。当窑运转时,椭圆对耐火砖造成机械应力,且椭圆度愈大所产生的机械应力也愈大。由椭圆度变化产生的剪切应力作用在每环砖的切线方向,故造成砖成环状剥落,见图 2。一般情况下,剥片厚度均匀、坚硬。
(2)回转窑的轴线偏移。回转窑是由轮带、托轮、托辊支撑的,其轴线应为窑各断面圆中心点的连线且在一条直线上,但在窑筒体安装及部分筒体切割更换后,或窑体经过一段时间运行后且窑内热工制度不稳定,在热负荷和荷重的作用下,窑体的轴线会产生偏移。之后,再经长时间的运转,轮带和托辊的磨损、托辊的外偏和内偏,各个支点的荷重条件会发生变化,特别是当支点的荷重过大时,容易造成托辊轴瓦烧损、轮带及托辊表面异常剥离或裂缝,这又将进一步加剧窑体轴线偏移;结果将使耐火砖受到挤压变形造成破损或脱落。耐火砖损坏后形状深浅不一,见图 3。
热应力对耐火砖使用寿命的影响
热应力是指当温度变化时,物体由于外在约束以及内部各部分之间的相互约束,使其不能完全自由胀缩而产生的应力。高温热膨胀,易使耐火砖产生轴向膨胀挤压应力,是窑内耐火砖剥落、破损的重要原因之一。以镁铬质或尖晶石质砖为例,1400℃时的膨胀率均可按 1.6%计算,长 198mm 的耐火砖其膨胀量可达3.17mm,如此大的膨胀,如果不能正确地留好环缝,过大或过小都将使耐火砖出现抽签、掉砖、剥落,严重缩短耐火砖的使用寿命。耐火砖因热应力产生破坏的形式见图 4。
生产操作对耐火材料使用寿命的影响
生产操作对耐火砖使用寿命的影响机理复杂且因素较多,现主要从以下两个方面进行分析。
(1)煅烧温度过高引起的砖损伤。新型干法预分解窑窑内火焰温度可达到 1700℃以上,另其过渡带、烧成带、冷却带、窑头罩、冷却机的喉部和高温区以及喷嘴外侧部位的工作温度也远高于传统窑相应部位的温度。即使采用优质耐火材料,大型回转窑的过渡带、烧成带和冷却带的窑衬寿命一般在0.5~ 1 年,短的甚至仅 3~5 个月;窑口和喷嘴衬料寿命一般只有 0.5~1 年,甚至更短;窑头罩和冷却机喉部窑衬寿命约 2 年。在试生产阶段,通常回转窑的运转率一般仅为 70%~75%甚至更低,极少数能达 85%~90%。如果再加上预热器、分解炉的运行状况不良,入窑物料分解程度很不稳定,会使窑内各工艺带位置经常变动,必将导致窑操作不稳定,窑衬损坏更快。例如若煅烧温度过高,就会引起窑内耐火砖损伤熔坑,见图5中圈出的部分。
(2)窑速较快引起的砖损伤。新型干法预分解窑的转速常达 3~3.7 r/min,甚至高达4 r/min 以上,回转窑筒体的线速度达到 1m/s 以上。在高转速、大直径和高温度的新型干法窑上,窑衬所受热应力、机械应力和化学侵蚀的综合破坏效应比传统窑要大得多。这就要求新型干法窑无论在冷态还是热态情况下,其窑衬均须具有足够的强度和稳定性。
延长耐火材料使用寿命的技术措施
椭圆度变形的控制
椭圆率是反映回转窑筒体椭圆变形程度的重要指标,公式如下(瑞士 Holderbank 公司最早提出):
式中: W—椭圆度;
Da — 窑的有效内径,m;
D —筒体外径,m;
σ— 筒体测示仪测得的最大偏差值, m。
瑞士 Holcim 公司(原名 Holderbank)提出的椭圆率管理数值,一般将其作为椭圆率的管理基准值,这个数值有上限值和下限值,与窑径呈直线关系,上限和下限之间的部分为理想范围,见图 6。上限值是对荷重或间隙引起的大窑变形而造成的耐火砖损伤所能允许的最大界限值,如果超过上限会给砖带来不良影响、造成砖脱落等事故,引起耐火砖破损。下限值是为了避免间隙不足时产生窑筒体被轮带夹住(所谓轮带夹紧现象)的数值。
实践表明,砖的损耗速度与热窑椭圆率有一定的相关性,通过它们的关系得到的近似公式(瑞士Holcim公司(原名 Holderbank)提出)。
W=1.22×0.002Dm+1.5V
W’=W/D×100%
式中: W’—— 椭圆率,%;
W——椭圆度;
Dm——轮带直径;
D——筒体直径;
V—— 滑移量。
计算得出:窑期(窑从开始运行至停产检修的时间)为 1 年时,热窑椭圆率的允许值应控制在0.42%以下,窑期为半年时,椭圆率要控制在 0.78%以下。但是,在烧成区域,由于椭圆度的增大会造成结皮不稳定,从而引起熔化损伤等异常损耗,所以对烧成带要进行更加严密的椭圆率管理。
椭圆率管理不仅对于稳定大窑操作、延长砖的使用寿命有重要的意义,而且通过定期测定热窑椭圆度也可以准确地掌握机械状况,从而能制定出更加准确的大窑维修计划。
回转窑轴线变形的控制
实际生产过程中,严格控制窑轴线偏移不得超过 3mm,否则必须进行纠偏处理。实践证明,当窑体在热态下轴线调整准确时,筒体的弯曲和扭曲都降到最小,各个支点上的荷重分布也比较适宜,窑内耐火砖、大窑筒体、轮带下垫板(座板)、轮带、支撑托辊、托辊轴、托辊轴瓦受到的压力较小;且耐火砖损耗速度明显下降,使用寿命明显延长,并能大幅度提高了窑的运转率。因此,必须加强热态下回转窑轴线的在线检测和偏移的及时纠偏工作。
大窑轴线的调整方法有两种:一种是在冷窑状况下,在大窑内部求出各个支点和大齿轮的轴心,使用光束,边调整托辊边将回转窑轴线调整在一条直线上;另一种是在回转窑在热态运行状态下,从大窑外部求出各个支点的回转轴心,然后边调整托辊边将回转窑轴线调整在一条直线上。实践证明,后者更加有效。
合理确定环缝尺寸以减小热应力的影响
环缝是回转窑进行耐火砖砌筑时,为减小高温时耐火砖膨胀产生轴向挤压应力对耐火砖的损坏而设置在每环耐火砖之间的间隙。环缝尺寸的大小,应根据耐火砖的线性膨胀系数、使用温度等通过计算确定。如通过计算,烧成带耐火砖的膨胀量为 3.17 mm,实 际 砌 筑 时 ,环缝尺寸 为 3.5 mm~4.0mm 之间;且各环缝间贴板可采用燃烧温度高的纤维板(日本耐材行业专用),并应研究烘窑操作制度,正常生产时也要控制热工制度稳定,以将轴向挤压力降为最小。
煅烧温度的控制
煅烧温度对耐火砖使用寿命的影响极为显著。因此,只有合理控制烧成温度,最大限度地延长耐火砖的使用寿命,提高窑的利用率、降低耐火材料消耗量,才能增产、降本。最高温度管理必须进入工艺管理过程,可结合火焰比色、测温仪、熟料晶相分析等方法进行测试。其中:火焰比色一般控制火焰温度 1500~1600℃;测温仪主要针对熟料落口温度进行控制,一般为 1320~1400℃;熟料晶相分析要控制 C3S的双折射率,一般控制为 0.007~0.008。
窑速的管理与控制
在生产操作过程中,不能一味地追求高转速提高熟料产量,要做到物料量、窑转速和窑内煅烧状况的匹配,才能达到最佳效果。同时可以根据熟料晶相的尺寸大小、生长状况,来判断窑速的控制值是否适宜。
总结
随着水泥工业应用的耐火材料品种不断增加,在注重节能降耗的今天,水泥生产企业应更多地了解耐火材料性能,合理使用耐火材料,采取一系列技术措施与控制,最大限度地延长耐火材料的使用寿命,把耐火材料消耗降到最低水平。通过对上述因素的技术控制与管理,耐火材料的使用寿命由原来的 8~ 10 月延长到现在的 14~ 16 个月,窑的运转率已超过85%~ 90%,熟料的产、质量均有所提高。
问题的提出
目前,我国的新型干法预分解窑生产技术已经成为水泥工业的发展主流,且已经进入大型化的发展通道, 5000t/d 及其以上规模的生产线是建设主流。众所周知,在煅烧过程中,熟料的烧成温度约为 1450 ℃,但窑内烧成带燃烧气体的温度最高可达 1700℃以上。如此高温的条件,对回转窑用耐火材料的要求也越来越高。
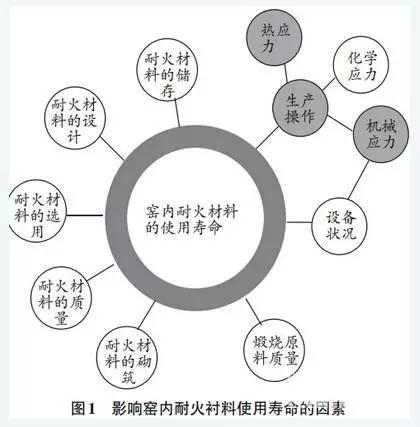
耐火材料使用寿命的影响因素
影响窑内耐火砖使用寿命的因素很多,见图1。通过理论分析结合实际生产经验,认为主要是三个方面,即机械应力作用、热应力作用和生产操作的影响。
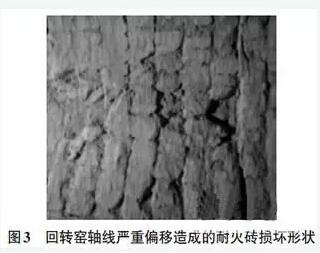
机械应力是物体由于外因变形时,在物体内各部分之间产生相互作用的内力,以抵抗这种外因的作用,并力图使物体从变形后的位置回复到变形前的位置。当窑内耐火砖所承受的机械应力超过其自身强度时,砖体在应力作用下产生局部或全部损坏。
产生机械应力的主要因素有以下两个原因:

(2)回转窑的轴线偏移。回转窑是由轮带、托轮、托辊支撑的,其轴线应为窑各断面圆中心点的连线且在一条直线上,但在窑筒体安装及部分筒体切割更换后,或窑体经过一段时间运行后且窑内热工制度不稳定,在热负荷和荷重的作用下,窑体的轴线会产生偏移。之后,再经长时间的运转,轮带和托辊的磨损、托辊的外偏和内偏,各个支点的荷重条件会发生变化,特别是当支点的荷重过大时,容易造成托辊轴瓦烧损、轮带及托辊表面异常剥离或裂缝,这又将进一步加剧窑体轴线偏移;结果将使耐火砖受到挤压变形造成破损或脱落。耐火砖损坏后形状深浅不一,见图 3。
热应力对耐火砖使用寿命的影响
热应力是指当温度变化时,物体由于外在约束以及内部各部分之间的相互约束,使其不能完全自由胀缩而产生的应力。高温热膨胀,易使耐火砖产生轴向膨胀挤压应力,是窑内耐火砖剥落、破损的重要原因之一。以镁铬质或尖晶石质砖为例,1400℃时的膨胀率均可按 1.6%计算,长 198mm 的耐火砖其膨胀量可达3.17mm,如此大的膨胀,如果不能正确地留好环缝,过大或过小都将使耐火砖出现抽签、掉砖、剥落,严重缩短耐火砖的使用寿命。耐火砖因热应力产生破坏的形式见图 4。
生产操作对耐火材料使用寿命的影响
生产操作对耐火砖使用寿命的影响机理复杂且因素较多,现主要从以下两个方面进行分析。
(1)煅烧温度过高引起的砖损伤。新型干法预分解窑窑内火焰温度可达到 1700℃以上,另其过渡带、烧成带、冷却带、窑头罩、冷却机的喉部和高温区以及喷嘴外侧部位的工作温度也远高于传统窑相应部位的温度。即使采用优质耐火材料,大型回转窑的过渡带、烧成带和冷却带的窑衬寿命一般在0.5~ 1 年,短的甚至仅 3~5 个月;窑口和喷嘴衬料寿命一般只有 0.5~1 年,甚至更短;窑头罩和冷却机喉部窑衬寿命约 2 年。在试生产阶段,通常回转窑的运转率一般仅为 70%~75%甚至更低,极少数能达 85%~90%。如果再加上预热器、分解炉的运行状况不良,入窑物料分解程度很不稳定,会使窑内各工艺带位置经常变动,必将导致窑操作不稳定,窑衬损坏更快。例如若煅烧温度过高,就会引起窑内耐火砖损伤熔坑,见图5中圈出的部分。
(2)窑速较快引起的砖损伤。新型干法预分解窑的转速常达 3~3.7 r/min,甚至高达4 r/min 以上,回转窑筒体的线速度达到 1m/s 以上。在高转速、大直径和高温度的新型干法窑上,窑衬所受热应力、机械应力和化学侵蚀的综合破坏效应比传统窑要大得多。这就要求新型干法窑无论在冷态还是热态情况下,其窑衬均须具有足够的强度和稳定性。
延长耐火材料使用寿命的技术措施
椭圆度变形的控制
椭圆率是反映回转窑筒体椭圆变形程度的重要指标,公式如下(瑞士 Holderbank 公司最早提出):
式中: W—椭圆度;
Da — 窑的有效内径,m;
D —筒体外径,m;
σ— 筒体测示仪测得的最大偏差值, m。
瑞士 Holcim 公司(原名 Holderbank)提出的椭圆率管理数值,一般将其作为椭圆率的管理基准值,这个数值有上限值和下限值,与窑径呈直线关系,上限和下限之间的部分为理想范围,见图 6。上限值是对荷重或间隙引起的大窑变形而造成的耐火砖损伤所能允许的最大界限值,如果超过上限会给砖带来不良影响、造成砖脱落等事故,引起耐火砖破损。下限值是为了避免间隙不足时产生窑筒体被轮带夹住(所谓轮带夹紧现象)的数值。
实践表明,砖的损耗速度与热窑椭圆率有一定的相关性,通过它们的关系得到的近似公式(瑞士Holcim公司(原名 Holderbank)提出)。
W=1.22×0.002Dm+1.5V
W’=W/D×100%
式中: W’—— 椭圆率,%;
W——椭圆度;
Dm——轮带直径;
D——筒体直径;
V—— 滑移量。
计算得出:窑期(窑从开始运行至停产检修的时间)为 1 年时,热窑椭圆率的允许值应控制在0.42%以下,窑期为半年时,椭圆率要控制在 0.78%以下。但是,在烧成区域,由于椭圆度的增大会造成结皮不稳定,从而引起熔化损伤等异常损耗,所以对烧成带要进行更加严密的椭圆率管理。
椭圆率管理不仅对于稳定大窑操作、延长砖的使用寿命有重要的意义,而且通过定期测定热窑椭圆度也可以准确地掌握机械状况,从而能制定出更加准确的大窑维修计划。
回转窑轴线变形的控制
实际生产过程中,严格控制窑轴线偏移不得超过 3mm,否则必须进行纠偏处理。实践证明,当窑体在热态下轴线调整准确时,筒体的弯曲和扭曲都降到最小,各个支点上的荷重分布也比较适宜,窑内耐火砖、大窑筒体、轮带下垫板(座板)、轮带、支撑托辊、托辊轴、托辊轴瓦受到的压力较小;且耐火砖损耗速度明显下降,使用寿命明显延长,并能大幅度提高了窑的运转率。因此,必须加强热态下回转窑轴线的在线检测和偏移的及时纠偏工作。
大窑轴线的调整方法有两种:一种是在冷窑状况下,在大窑内部求出各个支点和大齿轮的轴心,使用光束,边调整托辊边将回转窑轴线调整在一条直线上;另一种是在回转窑在热态运行状态下,从大窑外部求出各个支点的回转轴心,然后边调整托辊边将回转窑轴线调整在一条直线上。实践证明,后者更加有效。
合理确定环缝尺寸以减小热应力的影响
环缝是回转窑进行耐火砖砌筑时,为减小高温时耐火砖膨胀产生轴向挤压应力对耐火砖的损坏而设置在每环耐火砖之间的间隙。环缝尺寸的大小,应根据耐火砖的线性膨胀系数、使用温度等通过计算确定。如通过计算,烧成带耐火砖的膨胀量为 3.17 mm,实 际 砌 筑 时 ,环缝尺寸 为 3.5 mm~4.0mm 之间;且各环缝间贴板可采用燃烧温度高的纤维板(日本耐材行业专用),并应研究烘窑操作制度,正常生产时也要控制热工制度稳定,以将轴向挤压力降为最小。
煅烧温度的控制
煅烧温度对耐火砖使用寿命的影响极为显著。因此,只有合理控制烧成温度,最大限度地延长耐火砖的使用寿命,提高窑的利用率、降低耐火材料消耗量,才能增产、降本。最高温度管理必须进入工艺管理过程,可结合火焰比色、测温仪、熟料晶相分析等方法进行测试。其中:火焰比色一般控制火焰温度 1500~1600℃;测温仪主要针对熟料落口温度进行控制,一般为 1320~1400℃;熟料晶相分析要控制 C3S的双折射率,一般控制为 0.007~0.008。
窑速的管理与控制
在生产操作过程中,不能一味地追求高转速提高熟料产量,要做到物料量、窑转速和窑内煅烧状况的匹配,才能达到最佳效果。同时可以根据熟料晶相的尺寸大小、生长状况,来判断窑速的控制值是否适宜。
总结
随着水泥工业应用的耐火材料品种不断增加,在注重节能降耗的今天,水泥生产企业应更多地了解耐火材料性能,合理使用耐火材料,采取一系列技术措施与控制,最大限度地延长耐火材料的使用寿命,把耐火材料消耗降到最低水平。通过对上述因素的技术控制与管理,耐火材料的使用寿命由原来的 8~ 10 月延长到现在的 14~ 16 个月,窑的运转率已超过85%~ 90%,熟料的产、质量均有所提高。
上一篇:D1/3/5/7/9炼钢电炉顶用耐火砖形 下一篇:如何延长感应电炉炉龄(坩埚炉衬
TAG标签:
耐火砖
河南耐火砖
高铝砖
刚玉砖
耐火砖价格
河南耐火材料厂