国内外不少高炉使用含锌炼铁原料,锌对高炉的危害有的表现为炉身、炉顶或荒煤气管道部位结瘤;有的表现为破坏炉衬乃至炉壳,影响高炉寿命。减少锌对高炉砖衬的危害,多从研究减少锌的入炉量着手,对于高炉砖衬抵抗锌的侵蚀能力的研究鲜有文献报道。本文对锌与高炉砖衬反应进行了试验研究。
1锌与高炉砖衬反应试验
1.1试验方法
锌与高炉砖衬反应的试验方法参考高炉炭砖抗碱性试验方法(YB/T5213-2005),该方法试验试剂为无水碳酸钾和木炭,在1100℃下保温30h,以实验前后强度变化率、体积变化率和外观综合评价炭砖抗碱性好坏。
锌与高炉砖衬反应的试验试剂为金属锌和碳酸钙。在高炉高温区,由ZnO还原出的锌以锌蒸气形态扩散到砖衬表面,并通过气孔、裂纹渗透进入砖衬内部。选择金属锌是模拟以上反应产生的锌蒸气。Zn与CO2反应可生成ZnO,产生体积膨胀破坏砖衬。碳酸钾在高温下可分解产生CaO和CO2,将CO2用于模拟高炉内CO2和Zn的反应过程。碳酸钙分解产生的氧化钙对砖衬的破坏作用比氧化钾小很多,所以采用碳酸钙而不采用碳酸钾。由于金属锌较重,对两者比例进行了调整,由抗碱试验的55g(碳酸钾)∶55g(木炭)调整为95g(金属锌粉)∶75g(碳酸钙)。
1.2 1100℃锌与高炉砖衬反应试验
试验用砖衬材料选择高铝砖和炭砖,目的是比较二者的差异。高铝砖和炭砖分别制成30mm×30mm×30mm大小,将高铝砖或炭砖和试剂分别装入带盖石墨坩埚内,放入反应炉内,石墨坩埚埋碳保护,实验温度1100℃,并在此温度下保温30h。高铝砖和炭砖试验结果见表1。
不同炉衬侵蚀试验结果表明,高铝砖侵蚀试验后体积变化不大,为+0.01%~-0.33%,质量有所增加,平均增加2.51%,试验后强度下降超过10%,为-13.93%。锌与高铝砖有一定的相互作用,并影响高铝砖强度。炭砖试验后体积变化很小,试验后强度还有所增加。锌与炭砖不发生反应,对炭砖的破坏作用比较小。试验后样品化验分析结果见表2。
试验后试剂中含w(Zn)较少,为0.13%,主要为CaO,w(CaO)为68.98%,锌从坩埚中挥发逸出。高炉砖和炭砖中w(Zn)分别为0.92%和0.042%,高铝砖w(Zn)比炭砖高得多。试验结束取出石墨坩埚时发现:1)取热电偶时粘结较牢;2)石墨坩埚上部有粘结层,下部未粘结,也说明锌逸出石墨坩埚外。
1.3 920℃与高炉砖衬反应试验
1100℃下高铝砖和炭砖与锌反应试验表明,试验后锌从石墨坩埚中跑出。根据锌的沸点为907℃,碳酸钙的分解温度为897℃,将反应温度调整为920℃进行试验。其它条件同1100℃试验。试验结束取出石墨坩埚只出现轻微粘结现象,试验结果见表3。
920℃下高铝砖和炭砖与锌反应试验结果与1100℃类似,锌与高铝砖有一定的相互作用,并影响高铝砖强度,强度下降率由1100℃时的13.93%增加到18.20%。炭砖试验后强度还有所增加。
1.4锌先扩散渗透后氧化反应试验
一般认为,还原出来的锌蒸气渗入砖衬的砖缝、气孔和裂纹中,当有CO2或水汽时,在800~1000℃的温度条件下能生成ZnO,在砖体内发生这一反应时将产生体积膨胀,从而破坏砖衬。前面的模拟试验是将锌的渗透、锌与CO2反应同时进行,试验结果不是很理想。为此采用两温度阶段进一步试验模拟。第一阶段只加锌作试剂,模拟锌的扩散渗透过程,第一阶段试验结束后降温冷却,取出试样再进行加碳酸钙重新升温进行第二阶段试验,模拟锌与CO2反应过程。考虑到锌的沸点907℃,第一阶段试验温度选择920℃,让锌充分渗透到试样内。碳酸钙的分解温度为897℃,为提高锌与CO2反应速度,第二阶段试验温度选择950℃。两阶段试验保温时间均为10h。第一阶段试剂配比锌与木炭之比为95∶75;第二阶段碳酸钙与木炭之比为75∶75。锌先扩散渗透后氧化反应试验结果表明,高铝砖强度下降达到27.38%,对高铝砖有较大的破坏作用,锌对炭砖的作用仍比较小。
多次试验结果表明,锌与高铝砖有较强的化学反应,降低高铝砖强度,对高铝砖有一定的破坏作用,锌与高铝砖反应也是高炉炉身容易结厚的原因之一。锌与炭砖难以发生反应,但锌易渗入炭砖内部孔隙和裂纹中,在条件具备时锌氧化生成氧化锌,发生体积膨胀,破坏炭砖结构,后者在试验条件下锌和CO2容易逸出,难以模拟其过程。
1.5 2种不同锌含量炭砖抗碱试验
某高炉锌渗透侵蚀很严重,炉底最下层炭砖w(Zn)达42%,为分析锌对炭砖抗碱性影响,对2种不同w(Zn)的炭砖进行抗碱试验,1种炭砖w(Zn)为8.65%(1号),另1种w(Zn)为35.92%(2号),试验结果见表5。抗碱试验结果表明,2种炭砖抗碱性极差,表现在抗碱实验后试样粉化,强度下降率达到95.26%和96.70%,体积变化率极大,w(Zn)为8.65%的炭砖体积膨胀32.29%,w(Zn)为35.92%的炭砖体积膨胀8.89%,质量变化w(Zn)为8.65%的炭砖增加5.47%,w(Zn)为35.92%的炭砖减33.07%,说明锌的存在对炭砖的碱侵蚀有较强的促进作用。
2 锌氧化反应温度试验
2.1 锌氧化开始温度试验
上述模拟试验结果表明,锌与高铝质材料能产生反应破坏高铝砖结构,但锌对炭砖结构破坏作用较小。一般认为锌破坏炭砖是锌氧化生成氧化锌,产生体积膨胀,破坏炭砖结构。锌在高炉砖衬内很容易渗透,有些高炉炉底炭素捣打料中都渗有金属锌,但现场取样却发现锌主要以氧化锌的形式存在,说明锌在高炉一定条件下发生了氧化反应生成氧化锌。高炉炉内总体上为还原气氛,但局部区域可能存在CO2和水蒸气的氧化气氛。初步试验表明,用高炉气氛模拟锌被氧化的过程,几乎难以观察该反应发生。为此,本试验采
用二氧化碳模拟锌氧化过程,研究锌与二氧化碳氧化开始反应温度、反应温度范围,试验结果可能对分析锌对高炉炭砖的危害有一定参考作用。锌的氧化反应温度试验,采用炭砖氧化试验炉,参考YB/T5292-1999进行试验,该设备可以记录试样的质量变化,分析反应进行的程度。试验在二氧化碳气氛中进行,二氧化碳试验流量为5l/min,试验结果见图1。
从试验结果可以看出,在开始升温阶段由于失水,质量有微小的下降,到500℃左右质量开始增加,到800℃后质量变化不大,试验结束后发现表面锌已成为氧化锌,但表层下部仍为金属锌,800℃后锌是否发生氧化反应还需进一步试验。
2.2 800℃以后锌氧化反应试验
初步试验表明锌表面氧化为氧化锌后,形成1层覆盖保护层,下面的锌不能发生氧化反应。为此进行了800℃及更高温度下的锌氧化试验。试验开始温度为800℃左右,二氧化碳流量为5l/min。试验结果见图2。800~900℃质量增加较慢,900℃以后质量增加较快,960~1100℃反应速度又有所下降。
图3是在二氧化碳气氛下,800℃时间和质量的关系,由图3可以看出,即使在800℃时,也只是前20min增加较快,以后基本不变。
上述试验结果表明,锌在500~1100℃范围内在二氧化碳气氛下,均可以发生氧化反应生成氧化锌,导致高炉炭砖的破坏。
3 结语
1)锌与高铝砖和炭砖在1100℃、920℃及锌先扩散渗透后氧化反应试验结果均表明,锌对高铝砖有较强的破坏作用,对炭砖的破坏作用比较小,其原因是锌与高铝质材料能发生反应破坏高铝砖结构,锌破坏炭砖是锌氧化生成氧化锌,发生体积膨胀,破坏炭砖结构,后者在实验条件下锌和二氧化碳容易逸出,反应时间不够,难以模拟其过程。
2)对2种高锌含量炭砖进行了抗碱试验,试验结果表明,2种炭砖抗碱性极差,表现在抗碱试验后试样粉化,强度下降率达到95.26%和96.70%,说明锌的存在对炭砖的碱侵蚀有较强的促进作用。
3)锌氧化实验结果表明,锌在500~1100℃范围内,在二氧化碳气氛下,可以发生氧化反应生成氧化锌,导致高炉砖衬的破坏。
1锌与高炉砖衬反应试验
1.1试验方法
锌与高炉砖衬反应的试验方法参考高炉炭砖抗碱性试验方法(YB/T5213-2005),该方法试验试剂为无水碳酸钾和木炭,在1100℃下保温30h,以实验前后强度变化率、体积变化率和外观综合评价炭砖抗碱性好坏。
锌与高炉砖衬反应的试验试剂为金属锌和碳酸钙。在高炉高温区,由ZnO还原出的锌以锌蒸气形态扩散到砖衬表面,并通过气孔、裂纹渗透进入砖衬内部。选择金属锌是模拟以上反应产生的锌蒸气。Zn与CO2反应可生成ZnO,产生体积膨胀破坏砖衬。碳酸钾在高温下可分解产生CaO和CO2,将CO2用于模拟高炉内CO2和Zn的反应过程。碳酸钙分解产生的氧化钙对砖衬的破坏作用比氧化钾小很多,所以采用碳酸钙而不采用碳酸钾。由于金属锌较重,对两者比例进行了调整,由抗碱试验的55g(碳酸钾)∶55g(木炭)调整为95g(金属锌粉)∶75g(碳酸钙)。
1.2 1100℃锌与高炉砖衬反应试验
试验用砖衬材料选择高铝砖和炭砖,目的是比较二者的差异。高铝砖和炭砖分别制成30mm×30mm×30mm大小,将高铝砖或炭砖和试剂分别装入带盖石墨坩埚内,放入反应炉内,石墨坩埚埋碳保护,实验温度1100℃,并在此温度下保温30h。高铝砖和炭砖试验结果见表1。

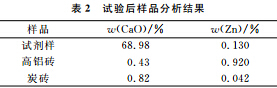
1.3 920℃与高炉砖衬反应试验
1100℃下高铝砖和炭砖与锌反应试验表明,试验后锌从石墨坩埚中跑出。根据锌的沸点为907℃,碳酸钙的分解温度为897℃,将反应温度调整为920℃进行试验。其它条件同1100℃试验。试验结束取出石墨坩埚只出现轻微粘结现象,试验结果见表3。

1.4锌先扩散渗透后氧化反应试验
一般认为,还原出来的锌蒸气渗入砖衬的砖缝、气孔和裂纹中,当有CO2或水汽时,在800~1000℃的温度条件下能生成ZnO,在砖体内发生这一反应时将产生体积膨胀,从而破坏砖衬。前面的模拟试验是将锌的渗透、锌与CO2反应同时进行,试验结果不是很理想。为此采用两温度阶段进一步试验模拟。第一阶段只加锌作试剂,模拟锌的扩散渗透过程,第一阶段试验结束后降温冷却,取出试样再进行加碳酸钙重新升温进行第二阶段试验,模拟锌与CO2反应过程。考虑到锌的沸点907℃,第一阶段试验温度选择920℃,让锌充分渗透到试样内。碳酸钙的分解温度为897℃,为提高锌与CO2反应速度,第二阶段试验温度选择950℃。两阶段试验保温时间均为10h。第一阶段试剂配比锌与木炭之比为95∶75;第二阶段碳酸钙与木炭之比为75∶75。锌先扩散渗透后氧化反应试验结果表明,高铝砖强度下降达到27.38%,对高铝砖有较大的破坏作用,锌对炭砖的作用仍比较小。

1.5 2种不同锌含量炭砖抗碱试验
某高炉锌渗透侵蚀很严重,炉底最下层炭砖w(Zn)达42%,为分析锌对炭砖抗碱性影响,对2种不同w(Zn)的炭砖进行抗碱试验,1种炭砖w(Zn)为8.65%(1号),另1种w(Zn)为35.92%(2号),试验结果见表5。抗碱试验结果表明,2种炭砖抗碱性极差,表现在抗碱实验后试样粉化,强度下降率达到95.26%和96.70%,体积变化率极大,w(Zn)为8.65%的炭砖体积膨胀32.29%,w(Zn)为35.92%的炭砖体积膨胀8.89%,质量变化w(Zn)为8.65%的炭砖增加5.47%,w(Zn)为35.92%的炭砖减33.07%,说明锌的存在对炭砖的碱侵蚀有较强的促进作用。

2.1 锌氧化开始温度试验
上述模拟试验结果表明,锌与高铝质材料能产生反应破坏高铝砖结构,但锌对炭砖结构破坏作用较小。一般认为锌破坏炭砖是锌氧化生成氧化锌,产生体积膨胀,破坏炭砖结构。锌在高炉砖衬内很容易渗透,有些高炉炉底炭素捣打料中都渗有金属锌,但现场取样却发现锌主要以氧化锌的形式存在,说明锌在高炉一定条件下发生了氧化反应生成氧化锌。高炉炉内总体上为还原气氛,但局部区域可能存在CO2和水蒸气的氧化气氛。初步试验表明,用高炉气氛模拟锌被氧化的过程,几乎难以观察该反应发生。为此,本试验采
用二氧化碳模拟锌氧化过程,研究锌与二氧化碳氧化开始反应温度、反应温度范围,试验结果可能对分析锌对高炉炭砖的危害有一定参考作用。锌的氧化反应温度试验,采用炭砖氧化试验炉,参考YB/T5292-1999进行试验,该设备可以记录试样的质量变化,分析反应进行的程度。试验在二氧化碳气氛中进行,二氧化碳试验流量为5l/min,试验结果见图1。
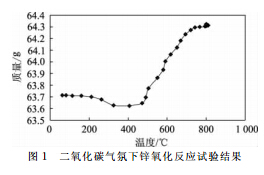
2.2 800℃以后锌氧化反应试验
初步试验表明锌表面氧化为氧化锌后,形成1层覆盖保护层,下面的锌不能发生氧化反应。为此进行了800℃及更高温度下的锌氧化试验。试验开始温度为800℃左右,二氧化碳流量为5l/min。试验结果见图2。800~900℃质量增加较慢,900℃以后质量增加较快,960~1100℃反应速度又有所下降。
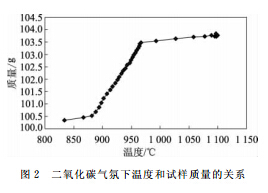
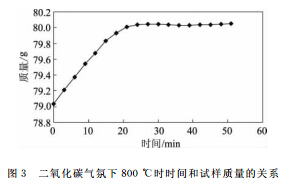
3 结语
1)锌与高铝砖和炭砖在1100℃、920℃及锌先扩散渗透后氧化反应试验结果均表明,锌对高铝砖有较强的破坏作用,对炭砖的破坏作用比较小,其原因是锌与高铝质材料能发生反应破坏高铝砖结构,锌破坏炭砖是锌氧化生成氧化锌,发生体积膨胀,破坏炭砖结构,后者在实验条件下锌和二氧化碳容易逸出,反应时间不够,难以模拟其过程。
2)对2种高锌含量炭砖进行了抗碱试验,试验结果表明,2种炭砖抗碱性极差,表现在抗碱试验后试样粉化,强度下降率达到95.26%和96.70%,说明锌的存在对炭砖的碱侵蚀有较强的促进作用。
3)锌氧化实验结果表明,锌在500~1100℃范围内,在二氧化碳气氛下,可以发生氧化反应生成氧化锌,导致高炉砖衬的破坏。
上一篇:熔块窑炉用耐火材料 下一篇:耐火隔热纤维与耐火砖比较及优点
TAG标签:
耐火砖
河南耐火砖
高铝砖
刚玉砖
耐火砖价格
河南耐火材料厂