耐火材料泥料的制取步骤,生产耐火砖的坯料(也称泥料)是把各种原料的粉料按一定比例配合,在混练机中加入水或其它结合剂而得到的混合料,它具有砖坏成型所需的性质,如可塑性和结合性。坏料的制备过程包括配料、混合等工序。
1、颗粒组成
颗粒组成的含义包括颗粒的临界尺寸、各粒级的百分含量等的确定
制成致密度高的坯料是耐火材料生产中的一个基本要求。理论计算和统计实验表明,单一尺寸的颗粒组成的泥料不能获得紧密堆积,只有高坯料内粗颗粒堆积形成的孔隙被较细颗粒所填充,后者形成的孔隙被更细的颗粒所填充时,才能达到坯料的紧密堆积。实际上,当有两种组分时,粗细颗粒的数量比为7:3,当有三种组分时为7:1:2时比较合适。在可能条件下,应适当增大临界颗粒尺寸,以使各组分颗粒尺寸相差大些。
在耐火材料生产中,通常多采取三种组分颗粒配合,即粗颗粒、中颗粒和细颗粒。但它们的粒径范围尚无统一标准,实际上它受原料的加热性质和其它条件的影响也难于固定不变。有如下的粒径范围可作为参考:
细颗粒:0~0.2mm(或0.1mm)
中颗粒:0.2(或0.1)~0.5mm
粗颗粒:0.5~4mm
2、配料
配料应注意下面几个问题:第一,配料的化学组成必须满足制品的要求,并且应比制品的指标要求高些。在化学组成中有包括对主成分的含量、易熔杂质总量和有害杂质的许可量的规定。第二,目前在生产中一般采用半干压制法,它要求的坯料应具有足够的结合性,因此在配料中应含有结合成分。第三,原料中含有水分和灼威成分时,使得原料、配料和制品的化学组成之间出现换算关系。
在实际配料中,通常采用重量配料法和容积配料法。
重量配料法是按物料重量比进行配料,此种方法使用比较普遍,其特点是精度高,误差不超过2%,易于实现自动控制,但在实际生产中应注意原料含水量波动带来的影响。目前采用的配料称量设备主要有手动称量秤、自动称量秤、称量车、电子秤和光电数字显示秤。
容积配料法是采用体积比配料。各种给料设备几乎都能适应作为容积配料的设备,其特点是配料设备简单,易于调节,可连续配料,有的密封性好,有利于防尘措施的实施,配料的精确度一般较差些。
3、混练
混练是将不同组分和粒度的物料与适量的结合剂混合,经搅拌、挤压等作用,制备成组分均匀和充分润湿的泥料的过程。其目的是使物料的成分和性质均匀,促进颗粒接触和塑化。
混练时的加料顺序对于泥料混合的均匀性影响很大。通常先加入粗颗粒,然后加水或泥浆、纸浆废液,混合1~2分钟后,再加细粉。否则,若粗细颗粒同时加入,易出现细粉集中成小泥团及“白料”,混练的时间随不同的机械设备和不同的物料而有所不同,一般混练时间短,均匀性差,时间太长则会因颗粒的再粉碎和泥料水分蒸发而影响成型性能,因此,要合理确定混练时间。在生产实践中,通常以检查泥料颗粒组成和水分含量以及灼减来评定其合格与否。混练好的泥料细粉形成一层薄膜包在粗颗粒周围,水分分布均匀,渗入颗粒孔隙之中,泥料密实,具有良好的塑性。
混练后的泥料在适当的温度和湿度条件下,贮放一段时间。这个工艺过程称为困料。在这个过程中,水分更加分布均匀,一直填充到毛细管空间,泥料的可塑性和结合性大大改应当指出,随着耐火材料生产工艺水平的提高和原料性能的改善,为了适应连续化大生产的需要,许多制品的生产中已取消了困料工序。
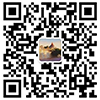