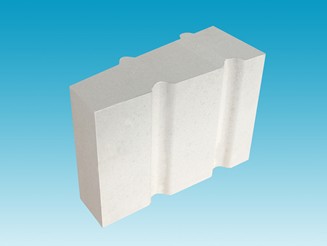
刚玉砖(sintered corundum brick)以致密的氧化铝熟料为原料制成的刚玉砖。该砖具有较高熔点,高温下性能稳定,常温及高温机械强度和耐磨性良好。抗金属侵蚀和抗氧化、还原性能优越。
生产刚玉砖所用原料是将高纯工业氧化铝经过煅烧后细磨(有时也加入少量MgO添加剂,以改善其晶体结构),压制成坯体,在1850℃以上煅烧。高温煅烧使坯体结构中气孔减少,晶粒增大约25~40倍。良好的烧结刚玉晶体呈致密的板状结构。
烧结刚玉砖生产工艺是将烧结刚玉分别破碎至3mm粗颗粒及部分小于0.074mm细粉,有的加入少量粘土及其它结合剂进行混练,用高压力摩擦压砖机或油压机成型,砖坯经烘干后装入高温窑内烧成。一般纯度较高的烧结刚玉砖,其烧成温度1750~1800℃。
如加入少量粘土或添加剂,烧成温度可在1600~1700℃。
TiO2、Fe203、MgO、CaO和R2O都是刚玉砖的杂质,这些杂质主要来自原料。还有原料磨细时带人的氧化铁。氧化铝中含有小于0.01%的TiO2,还有作为促进烧结的添加物或者硅酸铝原料的杂质,使TiO2含量达到l%—1.5%。TiO2及Fe203、FeO使刚玉砖的蠕变应力减小。
用磷酸盐结合的刚玉砖密实而坚固,引人P205小于3%,刚玉砖的耐火性质稍有降低,蠕变应力和断裂强度亦降低,因此受高温荷重作用的刚玉砖不宜引入P205。
般刚玉砖的气孔率大都在18%—23%。闭口气孔率在3%—6.6%之间波动,闭口气孔是刚玉结晶颗粒内的气孔。可以根据闭口气孔率增加程度考虑提高刚玉砖的密度。提高刚玉砖的密度,透气度降低,证明气孔尺寸减小。
刚玉熟料的煅烧温度及刚玉砖的烧成温度对刚玉砖的气孔率有决定性的影。向,其次泥料的颗粒组成、添加物和砖坯的成型压力对刚玉砖的气孔率都有重要影响。
刚玉熟料煅烧温度由1300℃升高到1750℃,纯刚玉砖的气孔率由3%—4%增大到15%—16%,而熟料煅烧温度由1300℃提高到1500℃,刚玉砖气孔率由3%—4%增大到8%—10%。降低刚玉制晶的烧成温度,同样使刚玉砖的气孔率增大,特别是刚玉砖烧成温度与所采用的刚玉熟料煅烧温度一样时,刚玉砖的气孔率增大很多。
泥料颗粒组成对刚玉砖气孔率的影响,主要是砖坯颗粒堆积密度的关系,而泥料的细颗粒数量对刚玉砖的烧结有重大影响。烧结刚玉熟料的临界颗粒尺寸由lmm增大到3mm,纯刚玉刚玉砖的气孔率稍有降低(降低1—3%),细颗粒含量由25%增加到45%及成型压力由25—30MPa增加到100MPa,有同样的影响。采用1000—1200MPa的成型压力,即使用电熔刚玉为主要原料,也能获得致密制品。
刚玉砖的抗热震性较差,因为大颗粒和细粉之间连结较好的致密结构,使刚玉砖的弹性模量相当大。
刚玉砖具有很强的抗渣性。对高炉炼铁熔渣,燃料渣、以及钢和铁的熔体很稳定。
刚玉砖有很宝贵的性质:在高温下有很好的抗碳还原稳定性。降低制品的气孔率和减少SiO2杂质含量,该性能显著提高。
刚玉砖的生产原料:
1:铝凡土,高岭土,粘土,硅藻土,主要有土组成,耐火性比较好。
2:石:莹石,蓝晶石,红柱石,镁橄榄石,蛭石,莫来石,叶蜡石,绿泥石,白云石,硅线石,镁铝尖晶石,硅石,主要有石材组成,耐火性较好。
3:陶砂,锆英砂,石英砂,镁砂,耐火性和石材相当。
4:铬矿,耐火性好。
5:金属铝粉,硅微粉,金属硅粉,刚玉砖,透气砖耐火性非常好。
6:沥青,石墨,酚醛树脂,珍珠岩,漂珠,赛隆,刚玉,硫酸硅,碳化硅,水玻璃,硅溶胶,碳化硼,铝酸钙水泥,氮化材料,页岩陶粒,氧化铝,铝溶胶,氧化锆等。
刚玉砖的优点性能:
1.具有较好的烧结活性,可以提高刚玉砖的致密程度;
2.板状刚玉的刚玉砖体积密度高,显气孔率低;
3.具有较高的常温耐压强度,常温抗折强度和高温抗折强度;
4.耐磨性能最好;
5.抗煤气化炉渣和渣油渣侵蚀和渗透性能优于纯电熔白刚玉砖;
6.作为骨料可提高刚玉砖的热震稳定性;
由于刚玉砖具有很好的高温性能,适用于各种各样的使用条件:不仅可以砌筑高炉炉胸,还可以用于高炉和其他窑炉的热风炉,1500—1700℃的炉墙、炉顶和格子砖;煤气预热器及分压低的,在碳、甲烷,天然气和焦炉煤气直接作用下的设备内衬和砖格子等;钢的炉外真空处理和连铸装置;对无烟煤和其他碳质材料进行高温处理连续作业的立式炉;高温炭化炉;高温荷重很大的窑炉;操作温度为1800℃的隧道窑及其他炉窑(低碱氧化铝为主的刚玉制品使用温度町达到1920—1950℃);作为催化剂和载热体喷嘴小球;沸腾炉风口带(如煅烧汞矿用);加热炉底;替代机器磨损快的金属部件和内衬,其中包括耐火材料工业;化学仪器和氨重整反应器的球状顶盖和内衬;生产玻璃球和玻璃纤维的高温玻璃熔窑顶和内衬。
二、刚玉砖砌筑专用泥浆
采用磷酸铝—矾土熟料泥浆。其泥浆组成为:
磷酸铝:矾土熟料=2:5
磷酸铝溶液由氢氧化铝、磷酸及水配制而成,要求Al2O3与P2O5的摩尔比为1:3.2(磷酸浓度为85%)。
矾土熟料级配:<0.3mm的占40%,通过4900孔筛的占60%。
应注意以下事项。
①所用矾土熟料应为一级高铝矾土,用回转窑经1600℃高温煅烧、加工而成。其微粉采用石衬球磨机加工,要求比表面积为4000—4500cm2/g。
②磷酸铝溶液配制步骤
a.按比例称取磷酸,氢氧化铝和水,把水倒入氢氧化铝中,不断搅拌。
b.将磷酸加热至70℃左右。
c.将氢氧化铝和水的浆体分数次加入到磷酸中并不断搅拌,直到溶液变清亮时为止。
d.溶液冷却后,经纱布过滤,注入容器中待用。
磷酸或溶液以及胶泥等所用的工具(搅拌棒、瓦刀、灰桶等)和容器均应用陶瓷质、搪瓷质、木材或不锈钢制成。不能用铁质或铝质等与酸易反应的容器和工具。
磷酸铝溶液相对密度应控制在1.56—1.59(20℃)。
若大量配制溶液时,可用冷配法,即将磷酸预先放在陶质大缸内,用开水调和氢氧化铝成浆体,分次加入到磷酸中去,边加边搅拌,等到加入的氢氧化铝浆体与磷酸的作用差不多完成时,再加入第2份、第3份……最后配成的溶液应是清亮的,然后测定相对密度进行调整。
③配制胶泥时,先将干料混合搅拌均匀,然后将磷酸铝溶液倒人干混合料中,再充分搅拌,即可使用。如采用铁磨细粉,则干混料中可不必加入氢氧化铝和耐火水泥,但混合料需在空气中搁置1昼夜,以利气体排出,方可使用。
④如作高温工业炉的修补,则预先将修补处进行处理,直至露出坚硬层为止,然后用毛刷或其它物品蘸取少量磷酸铝溶液,涂刷在修补处,湿润表面(不宜涂刷过多),然后进行修补。
如作胶泥使用,则预先需把被粘结件的表面尘土、油污去除,最好先把表面打毛,然后进行粘结。
⑤热处理的升温速度以不超过10—20℃/h为宜。