耐火砖成型方法是广泛普及的,成型砖坯的气孔率通常为20%~50%。成型气孔率小于10%的砖坯,没有获得成功。为了取得低气孔率的耐火砖,靠砖坯(半成品)烧成。用烧结法使气孔率降到指定值,并有可能使耐火砖达到理论密度范围。可是烧结的同时发生收缩,颗粒(晶体)尺寸和气孔尺寸增大,在许多场合算是有害的。成型和随后的烧结时间长(2~5天),也是劳动和动力消耗过程。在最短时问内解决最致密,同时又很坚固的耐火材料问题——耐火砖采用热压成型方法。热压成型包括粉料在砖模里直接烧热到必要的温度并压制。同时发生致密和烧结。
成型压力和温度限制了砖模的寿命。现在应用最多的是石墨模型。用感应方法或经石墨让电流通过的方法,使粉料在其中加热。石墨模型成型压力通常为lO~l5MPa。用碳化钛制的模型,温度800~900℃时,在14到21MPa压力下成型;用钼合金制的模型,在惰性气体介质中,低于1200℃的温度下,允许压力为14~21MPa;在刚玉模型中,温度为1100℃时,70~140MPa压力下成型,得到接近理论密度的耐火砖。
单一机理不能描述热压的整个过程。至少分为三个阶段。
开始阶段,致密根据别列日诺(A.C.Bepex(Horo)方程式,£~(tgp)-1,然而这个关系后来退化。
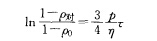
第二阶段,致密按粘滞流动机理进行,并用方程式描述。
式中,(ρ对)为相对密度,绝对致密时等于1;(ρo)为τ=0瞬息间的初始相对密度;η为成型温度下泥料
从宾汉粘滞流动公式得出方程式。在指定的时间τ,取得指定的相对密度,必须按方程式确定热压的压力p。同时初始(模中)相对密度用ρo试验确定。写出方程式形式In(1-ρ对)=3pτ/4η+C,式中C=In(1-ρo)=恒量,可以看出In(1-ρ对)与τ表现直线关系,又是粘滞流动的正式特征。按直线的倾度值可以确定粘度。为了得到致密的砖坯,更有效的降低粘度,均匀地提高温度,而不提高压力。因为提高温度,在粘度的实际范围通常降低一点儿,而压力可能要增大一个等级。热压时,可能某些颗粒增大,虽然还比烧结时小,可是粘度增大,因而致密降低。所以在成型前的配料中,适当引入抑制剂来减缓颗粒增长速度,随砖坯密度增加,方程式的项减少,而致密速度下降。
热压的最后阶段,致密动力学,或由时间的平方根,或由时间的立方根决定,代表的是扩散烧结。当△ρ对/Po~τ的平方根时,发生开口气孔愈合(排除),当△ρ对/Po~τ的立方根时,排除闭口气孔。所以,热压第三期间算是按扩散烧结机理产生致密。
热压时,又好像通常烧结时添加物的有效作用。例如:烧结Al2O3用MgO添加物(质量分数为0.02%~0.04%)的良好作用是毫无疑义的。氧化镁有如下作用:氧化铝离子聚集在氧化镁固熔体中,提高扩散系数并加速气孔的排除。使气孔尺寸减小和它的能动性增大,而且气孔被布置在颗粒边界上,本身更妨碍刚玉晶体的异常增长。
热压耐火砖与烧结耐火砖比较,当它们的气孔率相同时,强度和热导率高。热压耐火砖同样是抗热震性低。
耐火材料工业对耐火粘土和高岭土的热压成型很有兴趣,开发了生产工艺。
方法的实质是根据耐火粘土和高岭土的性质以及作为高温增塑剂,含的粘土组分和基于更耐火的骨料(锆英石,二氧化锆,石墨,氧化铝等)的复杂成分泥料,加热到高温变为可塑状态。更进一步理解的方法实质是热压利用液相烧结过程。
视为材料热塑状态的成型方法:同时过程的温度取决于成型系统性能的流变性(粘度,流变极限)。这个方法与热压的差别是粗坯在窑里预先加热到指定温度(同时形成某些数量的液相)后来它转移到模型中,并压制。第一阶段发生的致密,通常在液压机上成型,由于质点互相迁移。热压时,液相在质点周围形成薄膜,由于体积重量快速达到临界密度,在其下发生弹性变形,并中止致密。第二阶段的致密是在固定压力的保温时期,用比例τ的平方根描述,代表的是烧结过程动力学。下图为粘土材料热压成型的有代表性的沉淀曲线。获得某压力在b点开始沉淀,它由零a点增长到c点,然后仍旧不变。沉淀由b点到c点与压力相称的变化,然后逐渐降低而在d点中止。同时其质量在该条件密度达到最大。

b点的压力乃是位移的最大应力或蠕变极限Pk。可以用试验确定最佳温度和在这个温度下的Pk值。例如:
原料 某地粘土 某地高岭土
最合适温度/℃ 1300 1450
流变极限Pk/MPa 2.34 2.34
原来各种粘土热压成型最佳温度时的Pk值和这些粘土可塑状态(常温下)同样的Pk值相近。这就是说粘土和高岭土在热塑状态使本身成为宾汉体。如果在比流变极限温度高的温度下成型,那么发生肿胀,这说明溶解在液相中的气体膨胀,耐火砖几乎完全没有气体渗透性。
按物理化学性质,用两个种类不同的粘土,当时一种是细分散的粘土,而另一种是粗分散的粘土,热塑成型耐火砖,缓慢冷却,获得热稳定的耐火砖。这种耐火砖的热机械性质非常高。例如用某地粘土和某地高岭土制得的耐火砖的气孔率为2.5%~6.1%,耐压强度为85MPa,0.2MPa荷重软化温度为1520℃,加热到1000℃并随后在水中冷却的抗热震性为70次。
由许多成分的耐火材料:石墨粘土、碳化硅粘土、石墨碳化硅粘土等加入耐火粘土作为增塑剂,在热状态中成型能够取得低气孔率的耐火砖。这种耐火砖的特点是低透气性,高热震性和较高的强度。
硅酸铝耐火砖的工业规模热压成型尚未实现。对于热压新的不同作法还处在探讨阶段。
(1)动态热压:粗坯在窑内加热到指定温度,然后在秒钟份额期间内用锤再压成型的过程。当压力不小于1000MPa时,锤下致密时间0.01~0.001s。
(2)反应性热压:材料分解(脱碳或脱水)温度下热压。
(3)含碳氧化物材料热压:众所周知,碳加热到350~450℃时增塑,480~490℃时变硬。碳一氧化物的混合物加以热压,在碳热塑状态的温度下,细分散的氧化物被压入碳中,然后温度提高到500℃,使整个混合物焦化,具有石头般的强度。
(4)热等静压成型:按过程的物理学是热压的不同作法。按压力运用性质和热等静压成型过程的工艺方式,类似平常(冷处理)等静压成型。把等静压和热压的要素联合实行热等静压成型方法,主要由事实决定。通常热压耐火砖的形状比例可能极其有限。此外,热压方法的不足是砖模使用期限太短,砖模污染砖坯材料等。
热等静压成型在难烧结材料基础上能制造形状相对复杂的致密耐火砖,认为是很有前途的方法。
热等静压成型方法的实质是半成品(粗坯)预先造型,安放在高温外壳的砖箱中(例如用钢或耐热型难熔玻璃制的)真空处理和利用热惰性气体或熔化铅,在某些场合利用易熔玻璃的压力加以热压。
采用保证等静压力高的设备,提高成型材料温度时,实行热等静压过程。有的文献介绍:温度低于2750℃和压力300MPa下的热等静压成型方法。
最后应当指出热压比通常的烧结具有很大的潜在能力。然而需要采用复杂设备。
上一篇:提高镁铬砖抗热震性的方法与途径 下一篇:如何保护回转窑烧成带的耐火砖
TAG标签:
耐火砖
河南耐火砖
高铝砖
刚玉砖
耐火砖价格
河南耐火材料厂