本文根据多年来对大型水泥回转窑窑衬材料的使用情况以及各种材料的性能分析,研制适合大型水泥回转过渡带、分解带的新型窑衬材料高活性相结合复合砖。
研制背景
在新型干法水泥回转窑窑衬中,过渡带是窑内最易损毁的部位。由于窑内热工制度波动频繁,该处衬体的热端面始终处于浮窑皮和无窑皮状态,一方面受到窑皮及水泥料的侵蚀、磨损,另一方面承受频繁的热冲击,工作条件非常恶劣。
目前,新型干法水泥回转窑过渡带用材料通常为镁铝尖晶石砖、白云石砖、镁铝铬砖及抗剥落高铝砖等,其中日产2500吨以上的水泥回转窑过渡带大多采用镁铝尖晶石砖。镁铝尖晶石砖是以镁砂和尖晶石为原料,经高温烧成制得,其理化指标归纳见下表。
镁铝尖晶石砖在使用中表现出的损毁方式主要有以下几种:
1、受水泥材料的化学侵蚀。
2、因高温热膨胀率较大,导致衬体材料应力集中,出现镁铝尖晶石砖的热端剥落或棱角断裂。
3、自身强度不高,磨损速率过快。
4、尽管含有一定的镁铝尖晶石相,材料热震性得到改善,但由于是以MgO为主,热震稳定性仍存在不足;在受到频繁温度波动条件下,材料强度下降,加剧了磨损速率。
另外,由于镁铝尖晶石砖的导热系数较大,回转窑筒体表面温度较高,热量散失大、易损坏窑体,同时也影响现场操作。
根据镁铝尖晶石砖的损毁机理及过渡带工作条件,作为过渡带材料应具有如下优点:
1、抗水泥物料的化学侵蚀性好。
2、高温热膨胀率低,保证砌体材料使用中应力小,避免应力损伤。
3、热震稳定性好。
4、强度高,耐磨性好。
5、导热系数相对要低。
从过渡带材料应具有的优点出发,考虑到主要的损毁方式,研制一种新型的过渡带材料—高活性相结合复合砖。
理论基础
由过渡带用镁铝尖晶石砖的损毁机理可知,其主要的损毁为应力损伤、热震剥落和化学侵蚀,其中应力损伤和热震剥落常导致材料使用中出现层状脱落,使衬体材料厚度不能得到有效的利用,是较快的损毁方式;而这两种损毁机制是由材料本身的固有性质决定的。在以MgO为主体组份的材料中,MgO的热膨胀系数为15-16×10-6(200~1000℃),在氧化物系耐火原料中可以说是非常高的,所以,镁质材料在频繁的温度波动条件下,内部产生较大的结构应力,制品强度下降或发生应力损伤。
为从根本上减弱这种应力,可选用线膨胀系数(α)较低的原料。考虑到新型干法水泥回转窑过渡带的使用条件,可以选用以Al2O3为主的原料,其中优特矾土熟料在性价比方面比较适合。以MgO为主的镁铝尖晶石砖抗水泥料的侵蚀性较好,相比之下,以Al2O3为主的材料的抗侵蚀性则较弱,为此,在以优特矾土为主的材料组份中引入第二种材料A。A为惰性材料,不与水泥熟料等发生化学反应,不会被侵蚀,如此,在一定程度上弥补了高铝材料抗侵蚀性差的缺点,使其抗侵蚀性得到一定的保障;同时,A组份的线膨胀系数α较低,小于5.0×10-6(200~1000℃),这样就可以保证复合材料在温度波动条件下的体积稳定性,使材料具有较高的抗热冲击性能,同时也可以降低砌体应力,保持砌体的完整性,从而解决了过渡带用材料的热震损毁和应力损伤的问题。
由于A组份为惰性材料,与矾土熟料的反应活性很低,所以,单独将组份A与矾土熟料混合做成的制品是不会有强度的,也是无法使用的,为将二者有机地复合到一起,可采取两种方式:
其一,加入粘土类低耐火相材料,依靠粘土的烧结将二者固定到一起;但这是依靠低熔点液相的作用,而低熔点玻璃相的存在对材料的高温抗侵蚀性及抗磨损性都是非常 不利的。
其二,引入第三种材料HAP材料,HAP引入到矾土与惰性材料A的混合体中,经中温处理后转变为很有价值的高活性组份,而此高活性相组份仅存在于1200℃以下,作为一种过渡的中间相;持续的升温处理,则转化为该复合材料的高强度结合相,从而将矾土熟料与惰性组份A牢固地结合到一起。在高强度结合相形成的过程中没有液相的促进烧结作用,完全是固固反应机制,所以材料的强度较高,而且远高于镁铝尖晶石砖及镁铬砖;这对要求具有很好耐磨损性能的过渡带来说是非常有利的。
由于矾土熟料中含有近2.0%的铁,在烧成条件下,铁将与Al2O3、SiO2等构成液相存在,促进烧结,这一过程在以液相烧结机制为主的高温处理过程中是可以的,但在高活性相结合复合砖的高温烧成中却是不希望的。
引入HAP组份的高活性相结合复合砖的烧成过程中,应控制砖内氧分压Po2/Po<10-17MPa,如此,则矾土熟料中的杂质铁等便起不到液相形成的促进作用,也避免了形成的高强度结合相向液相中的溶解及二次再结晶,从而使材料保持较高的断裂韧性、高温强度及热震稳定性;同时,组份A也能够稳定存在,制品能够保持较好的抗水泥熟料的侵蚀性,所以,该复合砖完全可以取代镁铝尖晶石砖,其性能也优于镁铝尖晶石砖,在过渡带、冷却带上应用是可行的,也是很有希望的。
镁铬砖和镁铝尖晶石砖同属于富镁材料,共同的不足就是热膨胀率大、耐热冲击性不好。烧成带镁铬砖主要就是由于这两种因素的作用导致使用中出现的剥落损毁。过渡带与烧成带的工作条件有些近似,所以从理论上讲,该活性相结合复合砖在烧成带上的应用也是可以的,而且部分性能还将优于烧成镁铬砖。如果现场操作适当,寿命将高于镁铬砖。生产工艺
1.原料控制与颗粒级配
为了保证制品的质量,原料进厂后首先在本厂实验室进行成份及相关性能测试。
原料的颗粒级配是影响制品性能的主要因素之一。考虑到制品的综合性能,经过实验筛选,高活性相结合复合砖的临界颗粒尺寸以5~10mm为宜,粉料粒度以0.088~0.044mm为好。
高活性相结合复合砖采用机压成型。混练出的泥料质量对制品的性能影响很大,所以混练工序是很重要的工艺环节。具体操作为:
首先将颗粒料加入混练机中混练1~2分钟,然后加入临时结合剂混练1~2分钟,再加入粉料混练4~6分钟,泥料混练均匀后出料,此谓“初次混练”。为得到高质量坯体,需将“初次混练”的泥料进行“均化”处理后方能用于成型。所谓“均化”即是将经过“初次混练”过的泥料进行12~24小时的捆料后再进行二次混练工艺。
2.成型
成型设备采用300~600t压力机。成型冲压先轻后重,短程多打。根据坯体的体积和与成型方向的尺寸来确定冲压的次数:一般厚度<65mm冲压5~6次;厚度为65~68mm冲压6~10次;厚度>85mm冲压8~12次。要求坯体密实无磨面,无缺角少棱,坯体密度要求大于2.9~3.1g/cm3。
3.干燥与烧成
为了保证高活性相结合复合砖的成品质量,对坯体必须进行低温烘干,烘干洞进口温度在30~55℃,高温段80~110℃,出口温度65~75℃。坯体在烘干洞里维持16~20小时。坯体残余水份要小于1%,然后装入窑中进行烧成。由点燃到熄火的全过程用测温锥和热电偶控示。烧成温度为139~1450℃,保温8~12小时。
主要特点
高活性相结合复合砖与镁铝尖晶石砖的性能比较见下表。
从表中看出,除抗化学侵蚀性与镁铝尖晶石砖相当外,其余指标均优于镁铝尖晶石砖,由此得到高活性相结合砖的主要特点为:
(1) 抗水泥料的化学侵蚀性较好。
(2) 高温热膨胀率低,保证砌体材料使用中应力小,避免应力损坏。
(3) 热震稳定性好。
(4) 强度高,耐磨性好。
(5) 导热系数低。
高活性相结合复合砖烧成过程中没有液相的产生,完全依靠HAP组份中温阶段产生的固态高活性达到活性烧结,继而形成高强度结合相,避免了结合相向液相中溶解及二次再结晶,使材料保持了较高的断裂韧性、强度及热震稳定性;惰性组份A的引入,使得制品保持了较好的抗化学侵蚀性;另外,该砖的最大优点即是导热系数比镁铝尖晶石砖小得多,降低了回转窑筒体表面温度,减少了热量散失,节省了能源。
所以说,高活性相结合复合砖的性能优于镁铝尖晶石砖和直接结合镁铬砖,在水泥回转窑的过渡带和冷却带完全可以替代镁铝尖晶石砖及镁铬砖;如果现场操作适当,可在烧成带取代镁铬砖,而且还将具有比镁铬砖更好的抗剥落性能。

在新型干法水泥回转窑窑衬中,过渡带是窑内最易损毁的部位。由于窑内热工制度波动频繁,该处衬体的热端面始终处于浮窑皮和无窑皮状态,一方面受到窑皮及水泥料的侵蚀、磨损,另一方面承受频繁的热冲击,工作条件非常恶劣。
目前,新型干法水泥回转窑过渡带用材料通常为镁铝尖晶石砖、白云石砖、镁铝铬砖及抗剥落高铝砖等,其中日产2500吨以上的水泥回转窑过渡带大多采用镁铝尖晶石砖。镁铝尖晶石砖是以镁砂和尖晶石为原料,经高温烧成制得,其理化指标归纳见下表。
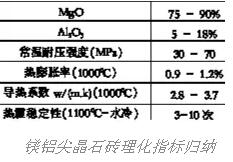
1、受水泥材料的化学侵蚀。
2、因高温热膨胀率较大,导致衬体材料应力集中,出现镁铝尖晶石砖的热端剥落或棱角断裂。
3、自身强度不高,磨损速率过快。
4、尽管含有一定的镁铝尖晶石相,材料热震性得到改善,但由于是以MgO为主,热震稳定性仍存在不足;在受到频繁温度波动条件下,材料强度下降,加剧了磨损速率。
另外,由于镁铝尖晶石砖的导热系数较大,回转窑筒体表面温度较高,热量散失大、易损坏窑体,同时也影响现场操作。
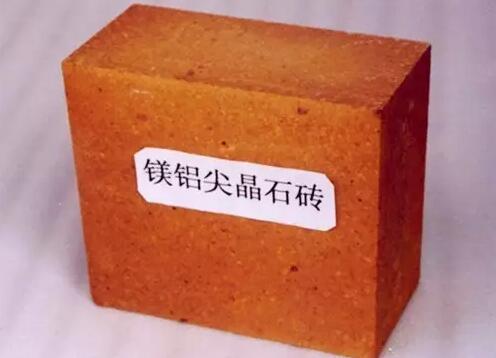
1、抗水泥物料的化学侵蚀性好。
2、高温热膨胀率低,保证砌体材料使用中应力小,避免应力损伤。
3、热震稳定性好。
4、强度高,耐磨性好。
5、导热系数相对要低。
从过渡带材料应具有的优点出发,考虑到主要的损毁方式,研制一种新型的过渡带材料—高活性相结合复合砖。

由过渡带用镁铝尖晶石砖的损毁机理可知,其主要的损毁为应力损伤、热震剥落和化学侵蚀,其中应力损伤和热震剥落常导致材料使用中出现层状脱落,使衬体材料厚度不能得到有效的利用,是较快的损毁方式;而这两种损毁机制是由材料本身的固有性质决定的。在以MgO为主体组份的材料中,MgO的热膨胀系数为15-16×10-6(200~1000℃),在氧化物系耐火原料中可以说是非常高的,所以,镁质材料在频繁的温度波动条件下,内部产生较大的结构应力,制品强度下降或发生应力损伤。
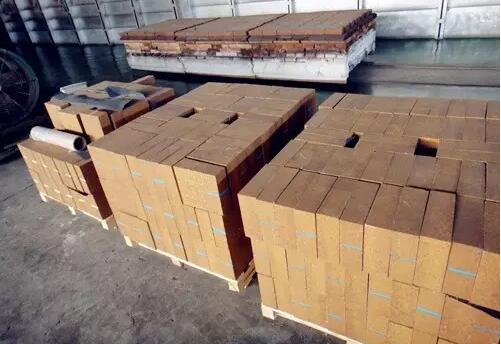
由于A组份为惰性材料,与矾土熟料的反应活性很低,所以,单独将组份A与矾土熟料混合做成的制品是不会有强度的,也是无法使用的,为将二者有机地复合到一起,可采取两种方式:
其一,加入粘土类低耐火相材料,依靠粘土的烧结将二者固定到一起;但这是依靠低熔点液相的作用,而低熔点玻璃相的存在对材料的高温抗侵蚀性及抗磨损性都是非常 不利的。
其二,引入第三种材料HAP材料,HAP引入到矾土与惰性材料A的混合体中,经中温处理后转变为很有价值的高活性组份,而此高活性相组份仅存在于1200℃以下,作为一种过渡的中间相;持续的升温处理,则转化为该复合材料的高强度结合相,从而将矾土熟料与惰性组份A牢固地结合到一起。在高强度结合相形成的过程中没有液相的促进烧结作用,完全是固固反应机制,所以材料的强度较高,而且远高于镁铝尖晶石砖及镁铬砖;这对要求具有很好耐磨损性能的过渡带来说是非常有利的。

引入HAP组份的高活性相结合复合砖的烧成过程中,应控制砖内氧分压Po2/Po<10-17MPa,如此,则矾土熟料中的杂质铁等便起不到液相形成的促进作用,也避免了形成的高强度结合相向液相中的溶解及二次再结晶,从而使材料保持较高的断裂韧性、高温强度及热震稳定性;同时,组份A也能够稳定存在,制品能够保持较好的抗水泥熟料的侵蚀性,所以,该复合砖完全可以取代镁铝尖晶石砖,其性能也优于镁铝尖晶石砖,在过渡带、冷却带上应用是可行的,也是很有希望的。
镁铬砖和镁铝尖晶石砖同属于富镁材料,共同的不足就是热膨胀率大、耐热冲击性不好。烧成带镁铬砖主要就是由于这两种因素的作用导致使用中出现的剥落损毁。过渡带与烧成带的工作条件有些近似,所以从理论上讲,该活性相结合复合砖在烧成带上的应用也是可以的,而且部分性能还将优于烧成镁铬砖。如果现场操作适当,寿命将高于镁铬砖。生产工艺
1.原料控制与颗粒级配
为了保证制品的质量,原料进厂后首先在本厂实验室进行成份及相关性能测试。
原料的颗粒级配是影响制品性能的主要因素之一。考虑到制品的综合性能,经过实验筛选,高活性相结合复合砖的临界颗粒尺寸以5~10mm为宜,粉料粒度以0.088~0.044mm为好。
高活性相结合复合砖采用机压成型。混练出的泥料质量对制品的性能影响很大,所以混练工序是很重要的工艺环节。具体操作为:
首先将颗粒料加入混练机中混练1~2分钟,然后加入临时结合剂混练1~2分钟,再加入粉料混练4~6分钟,泥料混练均匀后出料,此谓“初次混练”。为得到高质量坯体,需将“初次混练”的泥料进行“均化”处理后方能用于成型。所谓“均化”即是将经过“初次混练”过的泥料进行12~24小时的捆料后再进行二次混练工艺。

成型设备采用300~600t压力机。成型冲压先轻后重,短程多打。根据坯体的体积和与成型方向的尺寸来确定冲压的次数:一般厚度<65mm冲压5~6次;厚度为65~68mm冲压6~10次;厚度>85mm冲压8~12次。要求坯体密实无磨面,无缺角少棱,坯体密度要求大于2.9~3.1g/cm3。
3.干燥与烧成
为了保证高活性相结合复合砖的成品质量,对坯体必须进行低温烘干,烘干洞进口温度在30~55℃,高温段80~110℃,出口温度65~75℃。坯体在烘干洞里维持16~20小时。坯体残余水份要小于1%,然后装入窑中进行烧成。由点燃到熄火的全过程用测温锥和热电偶控示。烧成温度为139~1450℃,保温8~12小时。
主要特点
高活性相结合复合砖与镁铝尖晶石砖的性能比较见下表。
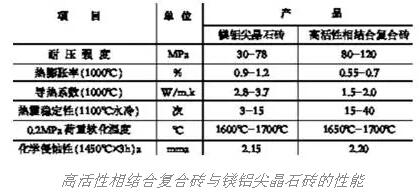
(1) 抗水泥料的化学侵蚀性较好。
(2) 高温热膨胀率低,保证砌体材料使用中应力小,避免应力损坏。
(3) 热震稳定性好。
(4) 强度高,耐磨性好。
(5) 导热系数低。
高活性相结合复合砖烧成过程中没有液相的产生,完全依靠HAP组份中温阶段产生的固态高活性达到活性烧结,继而形成高强度结合相,避免了结合相向液相中溶解及二次再结晶,使材料保持了较高的断裂韧性、强度及热震稳定性;惰性组份A的引入,使得制品保持了较好的抗化学侵蚀性;另外,该砖的最大优点即是导热系数比镁铝尖晶石砖小得多,降低了回转窑筒体表面温度,减少了热量散失,节省了能源。
所以说,高活性相结合复合砖的性能优于镁铝尖晶石砖和直接结合镁铬砖,在水泥回转窑的过渡带和冷却带完全可以替代镁铝尖晶石砖及镁铬砖;如果现场操作适当,可在烧成带取代镁铬砖,而且还将具有比镁铬砖更好的抗剥落性能。
上一篇:珍珠岩原材料产业发展回顾 下一篇:石墨粘土砖从原料到生产工艺的全
TAG标签:
耐火砖
河南耐火砖
高铝砖
刚玉砖
耐火砖价格
河南耐火材料厂